A conversation with Anupama Kundoo
Architecture creates more problems than it solves
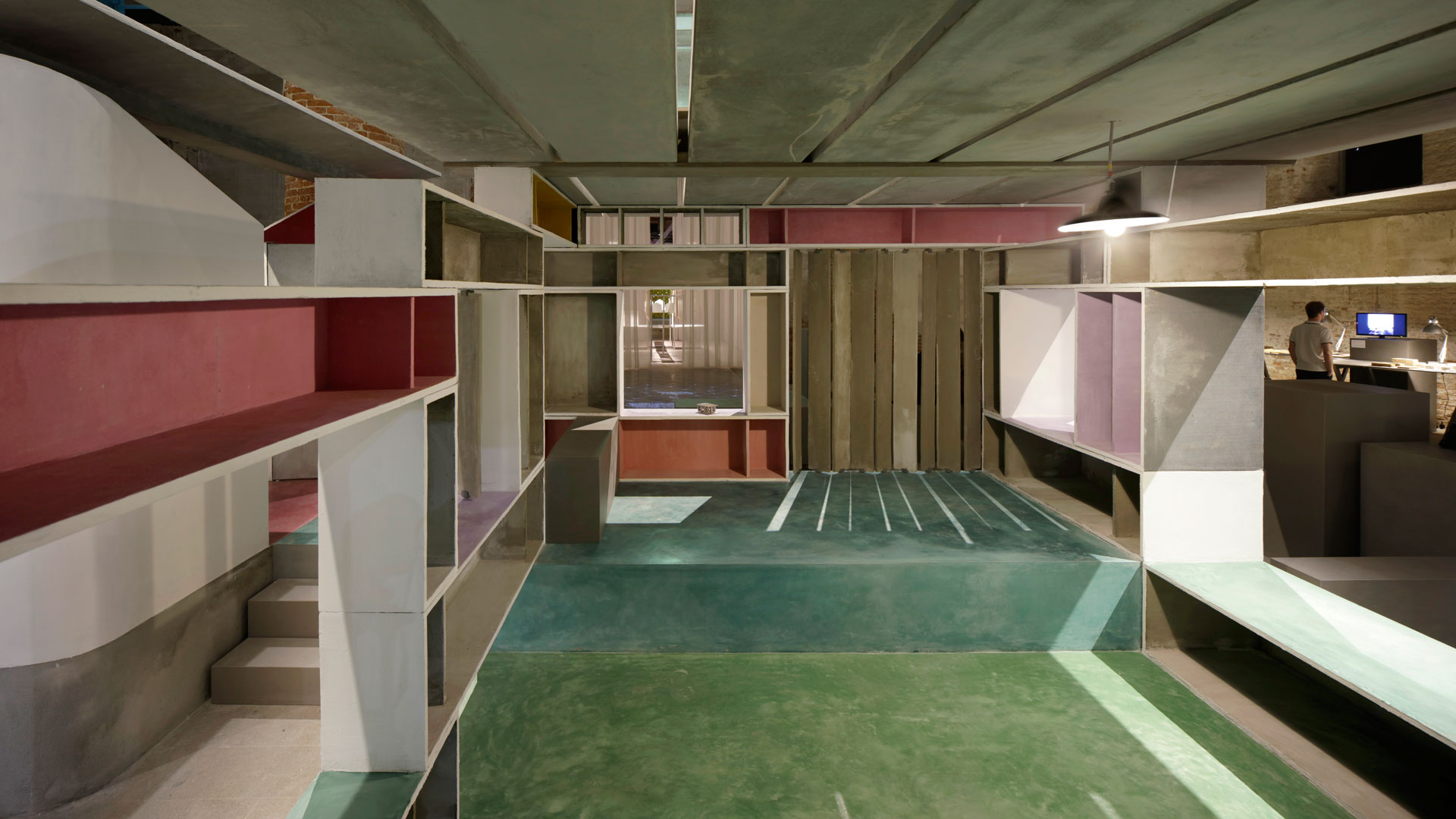
Anupama Kundoo is an architectural world traveller. She spreads her time between her office in the Indian town of Auroville and Madrid, where she holds a professorship for affordable housing. She studied in Mumbai and got her doctorate at TU Berlin. She is presenting at the Venice Biennale of Architecture for the second time since 2012. We met with Anupama Kundoo at the opening of the biennale in Venice to talk about low-tech, high-tech and how she wants to alleviate housing needs with a beacon of design.
At the 2016 Biennale of Architecture, you are presenting a house prototype called ‘Full Fill Home’. You’re using it to demonstrate the possibilities of ferrocement as a building material.
It was Pier Luigi Nervi who introduced ferrocement to mainstream architecture with his shell structures. He recognised that the intrinsic weight of concrete had a detrimental effect from a certain span width and tried to reduce the weight using ferrocement. It’s a material that can be made very thin; you don’t need more than two and a half centimetres.
You use chicken wire for reinforcement instead of steel. But it’s difficult to evaluate ferrocement structurally because the wire frame goes through everything. Unlike with steel-reinforced concrete, tension and pressure zones are not structurally separated. But ferrocement still has the same ingredients: steel, sand, cement, water. Only the gravel is missing. My hope is that ferrocement can be used to build more square metres with much lower use of material.
‘Full Fill Home’ is based on the principle of modularity. It’s created from ferrocement blocks.
The house is a conceivable application of modular building blocks. The blocks are hollow and we utilise this space for storage or furniture. The usable space of the home stretches into the empty space in the blocks. The house therefore seems to be bigger than it is – it’s actually just three by five metres. You have a bed, a kitchen block, everything you need. ‘Full Fill Home’ is a simple solution to the complex and arduous problem of providing housing
The production is low-tech; builders can easily produce the ferrocement elements themselves. It can be built within a week. But this house is not a universal solution; we designed it for the tropical climate of southern India, which is why it is so open.
The production of the house is low-tech, but the concept behind it involves German high-tech engineering. We are working with Mike Schlaich from the Institute of Civil Engineering at TU Berlin on this project.
Our aim is to use as little material as possible. We brought craftspeople from India to a workshop in Berlin to work with Schlaich and his students on further developing the ferrocement modules. After all, if you work the material with a high degree of skill, you can exploit its properties even better. For example, we experimented with textiles as a reinforcement material. Several of the blocks have remained in Berlin and are being experimented with further. The project is enriching for everyone involved – it’s interdisciplinary and intercultural.
You spoke about your interest in calls for tenders. How would you describe the German tendering system?
It’s a huge problem, not just from a political point of view, but also from a cultural building perspective. The tendering world is full of incestuous relationships. What I mean is that it’s always the same players in the game. Nothing can really happen in this type of situation. You see certain design types submitted again and again over a period of three, four years and then they die down. There’s no real contribution to the building culture! Because the requirements get more and more detailed: we have to calculate facade areas and write pages and pages on barrier-free construction. Then along comes an entire army of assessors who review the whole thing in the evaluation phase and then submit a report to the panel of judges where they say a design is ‘barrier-free but to a limited extent’
Who does that benefit? They spend 6,000 or 7,000 euros to get this determination – and that’s not even taking into account the costs of the architects. It’s completely useless for an architectural concept.
Where did this obsession with detail come from?
The clients want to cover themselves in all directions. I think that’s the main reason why calls for tenders today are no longer drivers of innovation like they were before. Architects are shackled by the huge catalogue of requirements they have to meet and have much less time to spend on their concepts.
What is your opinion of the restricted access to calls for tender – and therefore the reduced opportunities for young architects to win contracts?
We've been having this debate for years, but our opinion is that there are always ways to get by. When you’re a young firm, you can join forces with established architects, which is what just happened in the call for tenders for the Bundestag visitors centre. Two young architects worked together with a larger firm and won the bid. The complaints about not having access are somewhat exaggerated. Before when my brother and I did not yet have our licensed architect stamp, we found someone to apply their stamp on our behalf. But we are advocates of open competition. Our theory is that if all calls for tender are open, the numbers of participants will regulate themselves.
To spread your concept, you need partners.
Definitely. Housing is a problem that you cannot solve alone. For us the project is a beacon of design: we are showing what we can do and hoping that others see it.
The industry has already started paying attention, and that is important. We built and exhibited a further prototype in India. At the moment we are testing it in our office.
We also have an order to build twenty of these houses. But the ‘Full Fill Home’ is just the start. Ferrocement has so much more potential.